Barcode Blues: How Barcode Fails Can Cripple The Auto Supply Chain
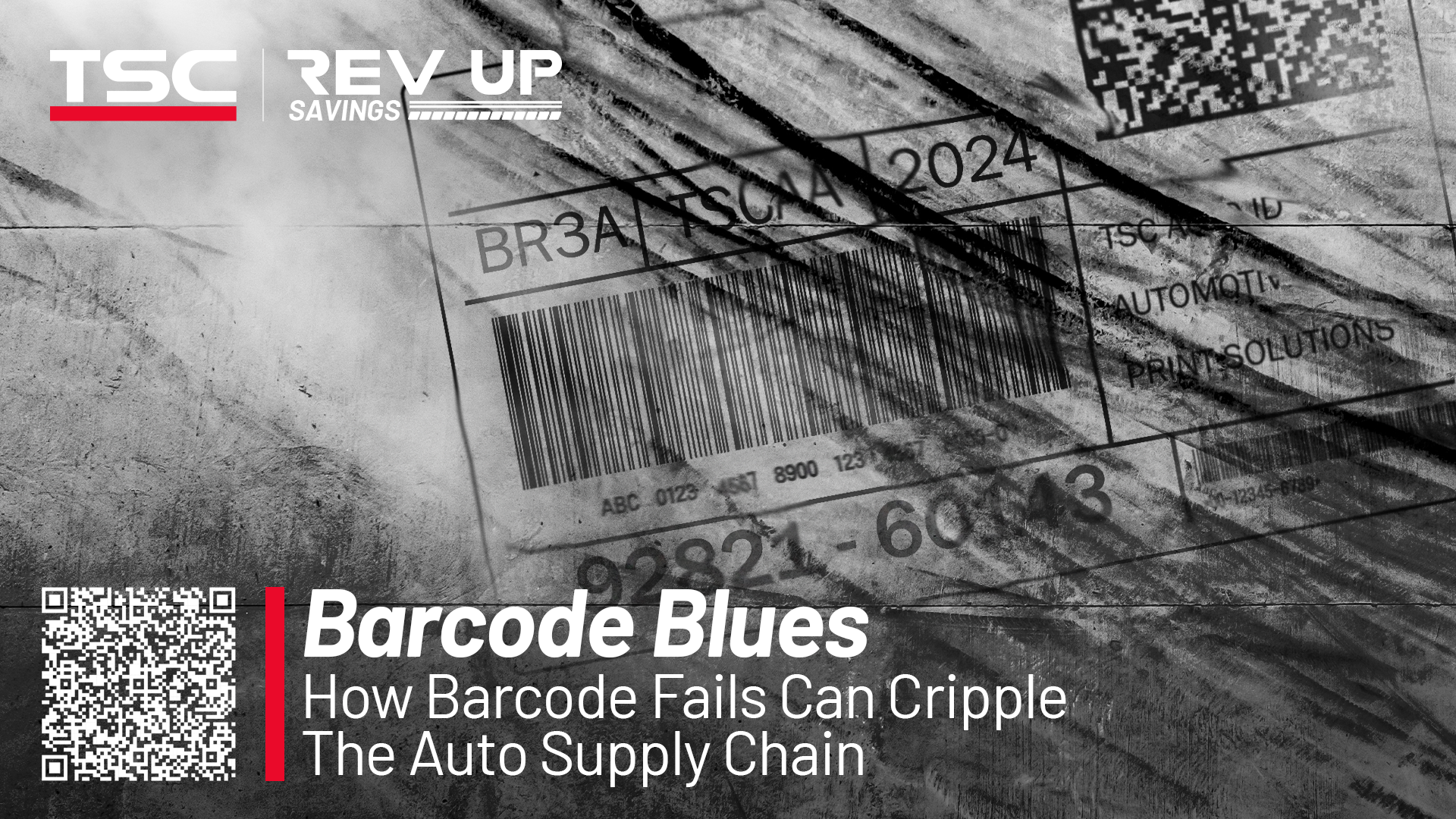
In any efficient or semi-automated process, mistakes can be extremely disruptive to workflows and costly to resolve. Specifically, in the case of barcode failures in the automotive supply chain, the consequences include:
- Carrier losses during shipment and undeliverable packages
- Unknown locations for received goods
- Incorrect inventory levels in customers’ ERP database
- Customer chargebacks or fees
- Failure in automated equipment relying on machine vision that imperil workflows
- Customer complaints leading to poor customer satisfaction and retention
- Downtime and rework required to fix labeling issues
- Failure to trace and confine small manufacturing nonconformance issues
The good news is that most of these concerns can be mitigated by employing a barcode inspection system using 100% verification. Not only does barcode verification prevent the issuance of unreadable codes, but it also serves as a quality engineer to understand why the code is failing and can identify the need for preventative maintenance or other necessary interventions before more serious effects occur. With the right system you can provide control charting for all your printers without hiring additional engineers.
What causes bad scans or unreadable codes?
ISO standards 15415 and 15416 provide for a grading system for 1D and 2D symbology, respectively, that allow investigators to precisely know the cause of barcode failures. Generally these come down to printer settings and configurations, the label design and code, and media and ribbon quality. You don’t have to be a grease monkey to know precisely where under the hood to look for your quality issues. Causes for unscannable codes can be ascribed to one of the parameters shown in Table 1 and each one is automatically measured and reported for each of up to 50 barcodes/label using the ODV-2D.
Table 1. Parameters Impacting Barcode Quality under ISO 15415/15416
Parameter | Code Types | Description | Causes & Interventions |
Decode | 1D/2D | Pass/Fail barcode reading | Ink bleeding, improper burn temperature |
Symbol contrast | 1D/2D | Difference in contrast between white and black bars | Uneven print head pressure, dirty printhead, poor quality labels, ribbon issues |
Min. reflectance | 1D | Measure of darkness of black bars | Poor ribbon quality from vendor, printhead burn temp |
Min. edge contrast | 1D | Contrast between adjacent bars/spaces | Uneven printhead pressure |
Modulation | 1D/2D | Variation in bar widths, positions | Data source issue, label format or calibration issue |
Defects | 1D | Looks for irregularities in the pattern | Dirty printhead or platen roller |
Decodability | 1D | How close is the pattern to ideal dimensions | Bad barcode image, quiet zone violations |
Fixed Pattern Damage | 2D | Damage to marker points or quiet zones defined by symbology | Ribbon wrinkling, label defects, dirt or debris, label design issues |
Axial Non-uniformity | 2D | Measure of dimensional skew between X & Y axes | Image compression or emulation issues |
Grid Non-uniformity | 2D | Measure of grid distortion or stretching | Label template corruption |
Unused Error Correction | 2D | Measure of redundancy needed to still read code | Indicates defects or combinations of other parameters present |
Grading 100% of your labels along these dimensions may seem like a daunting task, but we’ve automated it for you in our online data verification (ODV) barcode inspection systems. The latest system is our ODV-2D, a fully integrated solution, with the ability to print, verify, and validate 1D and 2D barcodes. Specifically, this system:
- Grades up to 50 barcodes per label including the most common 1D (Code 39, Code 93, Code 128, UPC/EAN) and 2D Datamatrix (Square, Rectangle), PDF 417, QR) symbologies
- Grades during printing at up to 8 inches per second (IPS)
- Can grade labels and forms up to 6.5” wide
- Can resolve X-dimension features down to 10 (mils) or roughly 250 microns
- Overstrike poor quality labels and automatically reprint based on thresholds defined by your team
The affordable ODV-2D unit installs on T8000 or T6000e printers and can be purchased preinstalled for easier calibration. It is the first system that grades barcodes to ISO 15415,15416 and 15426 standards and stores a detailed report of each transaction for audit purposes providing evidence of your high-quality standards to your customers.
Success Story: Motorcycle Manufacturing
An automotive parts manufacturer was labeling small components with multiple 2D barcodes to densely share traceability data downstream with Tier 1 customers. The data was hard to read downstream and was causing product returns and poor customer satisfaction. Using ODV-2D on a T6000e printer we revealed multiple quiet zone violations that can yield poor and inconsistent decoding. We helped them adjust the size of the barcodes in their label design and set them up with ODV-2D systems to ensure even small size Data Matrix codes are able to be graded down to 250 micron features saving valuable time and money.
Learn More
Want to dive deeper? Find out how other manufacturers in the automotive market are using online data verification to reduce errors, save money, and maximize productivity and equipment uptime.
We’ll show you how in-depth, over the coming weeks, in this comprehensive Blog series ‘Rev Up Your Savings.’
Or, please visit our Automotive Solutions web page anytime!
Contact Us
Click here to schedule a free consultation.