How Integrated Barcode Inspection Helps Suppliers Save Money, Reduce Returns, and Avoid Wreaking Havoc in the Supply Chain
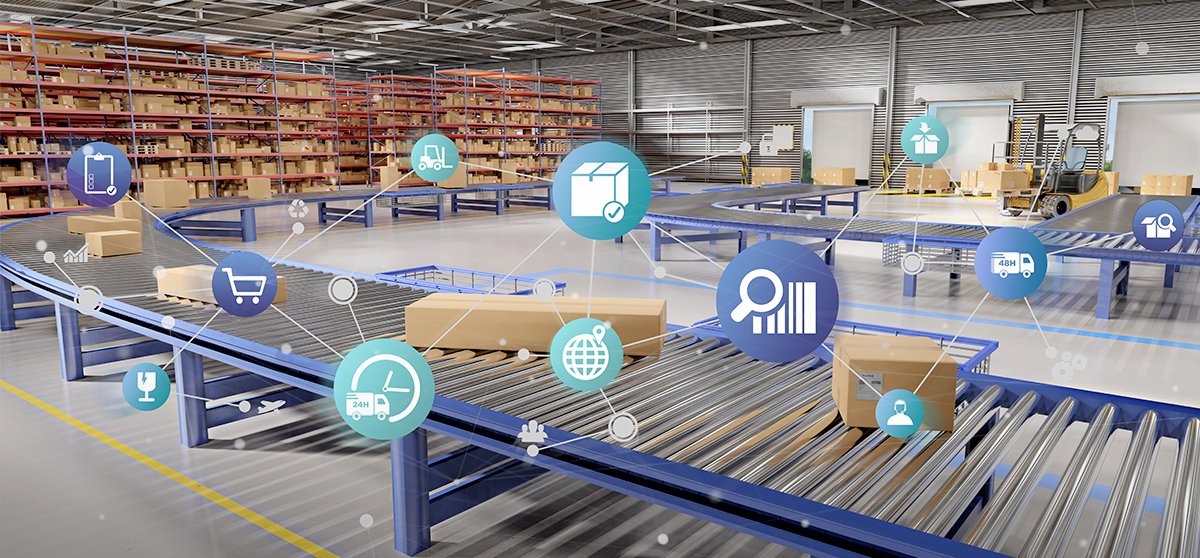
All it takes to create a major supply chain and production issue is not having the right part, at the right location, at the right time. For example, a shortage of computer chips impacts the number of cars being made. According to Computer World, in 2021 “the dearth of computer chips forced auto manufacturers to close down manufacturing and cut production by as much as 7.7 million cars.” Quite a significant reduction! Delays at ports are also impacting availability of items in stores.
The supply chain relies on multiple players and a broken link wreaks havoc. As a supplier, you do not want to be the reason your customer’s warehouse operations have been delayed. Being the cause of these delays and shutting down a customer’s manufacturing line is problematic. Not to mention, expensive. Manufacturers are increasingly anxious to share their pain with those that have caused this issue, especially if the delay is preventable, in the form of fines and other penalties.
Using our automated barcode inspection systems, suppliers can save money and reduce returns and other costly penalties. Keep reading to learn more about the challenges with bad barcodes and how the solution can help suppliers increase efficiency and peace of mind for you and your downstream customers.
Bad Barcodes Make Processing Time Consuming
Incoming goods are scanned and the information from the barcode label directs the forklift driver on where to place the pallet. Increasingly, automated transports are used in this capacity due to the high volume. If the barcode label isn’t read automatically and successfully, the process comes to a halt. Manual procedures then kick in and the pallet is re-routed to a holding area in order to prevent a slowdown in processing other incoming pallets.
Manual processing takes time, holds up incoming goods, and causes unnecessary delays for critical items needed on the production line. Impacting your customer’s receiving process, and potentially their manufacturing process, can result in chargebacks, fines, audits, or goods being returned. With heightened pressure on the supply chain, it’s critical to reduce any controllable errors with barcode labels.
Manual Spot Checks Make It Difficult to Inspect Every Barcode
Does inspecting every barcode on every label sound daunting? It won’t be with the right tools. With the right barcode inspection system, it’s actually far easier than doing spot checks! If you’re shipping tens of thousands of pallets every month to your customers, adding a spot check station requires a scanner, a PC as the controller, software, and someone to perform the test. If a bad label is found, how do you flag it so it’s not used and is reprinted? If the label is already on a box, how do you return the box to the label area so a replacement can be reprinted?
Manual inspection is not efficient, and it requires additional space, equipment, and labor. It could also require possible recirculation lines in the conveyor process. If the label error rate is low, chances of catching the error with a spot check is virtually nil. All the space and expense is doing nothing to reduce the likelihood of catching potential errors.
Is there a simpler solution? Yes. Keep reading to learn all about it.
Automated Barcode Inspection Printers for Easy Validation of Every Barcode
TSC Printronix Auto ID Enterprise Industrial Printers with integrated barcode inspection automatically locate and grade every barcode on every label for every job without an operator’s intervention on a wide range of printer data streams. There is no need for additional templates, servers, software, separate devices, or modifications to your printers. If an unacceptable barcode is found, the label is automatically retracted, overstruck, and a new one is printed without operator intervention. This saves time, money, and ensures your business continues to operate at full capacity without any setbacks or hold ups. It also ensures you’ll be delivering easy to read barcode labels to your downstream customers, eliminating any holdups to their processing that could lead to a fine for you.
Our T8000 and T6000e Enterprise Industrial ODV-2D Printers come equipped with our unique integrated barcode inspection system to automatically verify and validate every single barcode label printed. These printers come equipped with numerous benefits that will enhance your operations and eliminate issues that affect your part of the supply chain. You can focus on what you do best, and let the printer automate label printing, grading, and inspection.
Expedite Processing with Barcode Inspection Printers
Using integrated barcode label inspection printers from TSC Printronix Auto ID, you can rest easy knowing that your shipments aren’t causing any delays in your customers’ receiving process. Automatic locating and fixing bad barcode labels enables operators to focus on the manufacturing process flowing smoothly. These Enterprise Industrial ODV-2D Printers help you prevent delays and product rerouting, and ensure your customers receive their goods on time.
Learn more about our barcode inspection printers on our website, or contact your local TSC Printronix Auto ID representative to get started.